bonner1040
Nick from Ohio
TreeStuff, Rock Exotica and All Gear are building a large drop structure called the Vertical Test Environment. Rock Exotica and All Gear have partnered with us on the VTE in order to help drive testing and demonstration to a new level.
We plan to use the VTE not only for dynamic drop testing, but for live demo. We will have the ability to install tree branches onto the VTE and then cut them, using similar branches placed the same way to perform repeat examples showing multiple methods for the same scenario.
Here are some 3d Renders of what we are building.
Thoughts? Criticism? Questions?
We plan to use the VTE not only for dynamic drop testing, but for live demo. We will have the ability to install tree branches onto the VTE and then cut them, using similar branches placed the same way to perform repeat examples showing multiple methods for the same scenario.
Here are some 3d Renders of what we are building.
Thoughts? Criticism? Questions?
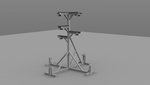
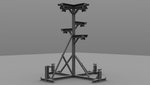
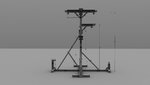
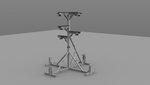