Burnham
Woods walker
Today I was buzzing up some limbs and such for the woodpile with my 200 rear handle. After a while, needed fuel and oil plus a small adjustment to tighten the chain.
I loosened the bar nut, then as I attempted to insert the scrench into the bar adjuster screwhead I was stymied by a bit of plastic and the edge of the insert. Closer examination showed that the metal insert that the bar stud goes through had spun a bit, tearing some plastic of the clutch cover.
Here's a few pictures.
I loosened the bar nut, then as I attempted to insert the scrench into the bar adjuster screwhead I was stymied by a bit of plastic and the edge of the insert. Closer examination showed that the metal insert that the bar stud goes through had spun a bit, tearing some plastic of the clutch cover.
Here's a few pictures.
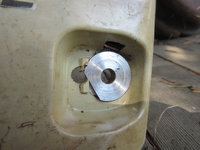
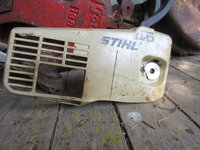
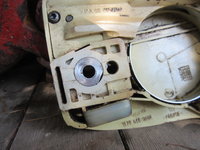
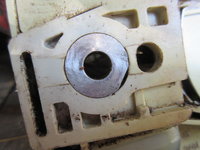