lumberjack
Young man on the go
This is a rare adapter, produced by GM between 1973-1975. It mounts the SM465 transmission with the NP 203 transfer case as shortly as possible.
The notch in the top hole, and the D shaped blind hole will be added when I get the measurements off the tranny.
The one made from plate and tubing is 2lbs heavier before welding than the cast version. The cross tube can be made a number of ways, and the mounting would be left to the discretion of the end user of the adapter.
Accuracy to +/- .005".
The notch in the top hole, and the D shaped blind hole will be added when I get the measurements off the tranny.
The one made from plate and tubing is 2lbs heavier before welding than the cast version. The cross tube can be made a number of ways, and the mounting would be left to the discretion of the end user of the adapter.
Accuracy to +/- .005".

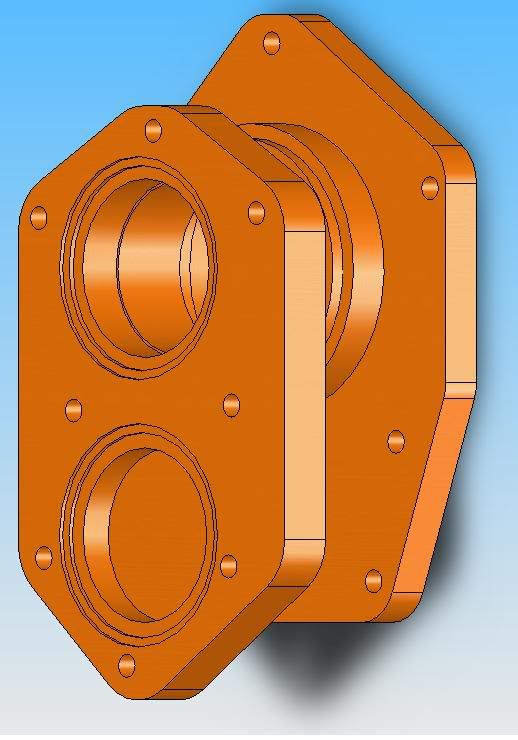
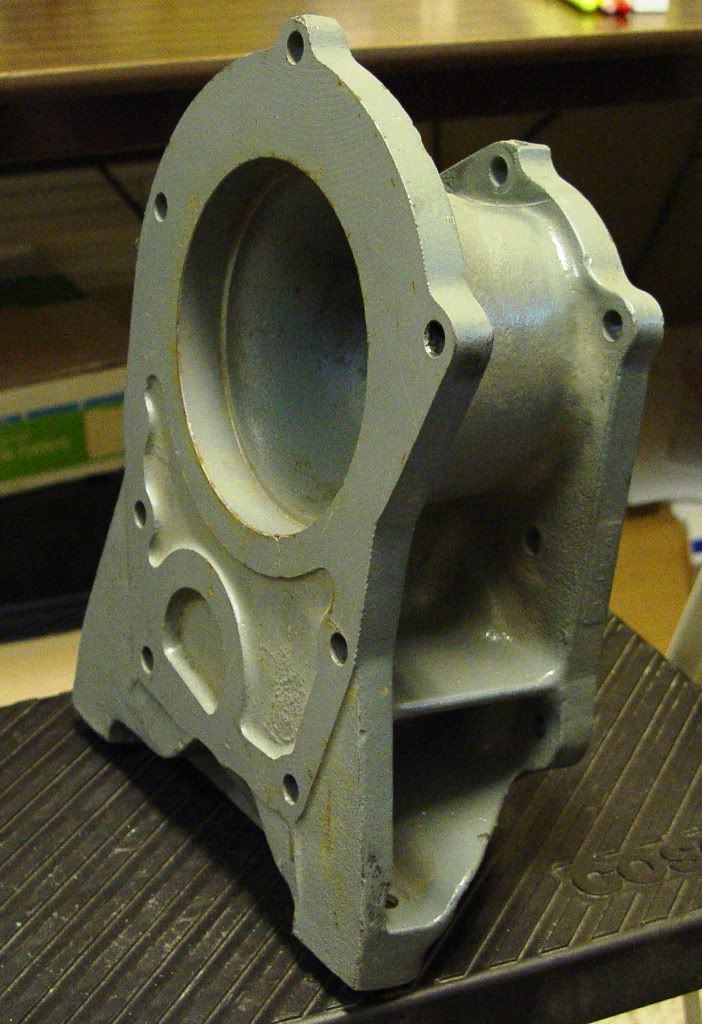
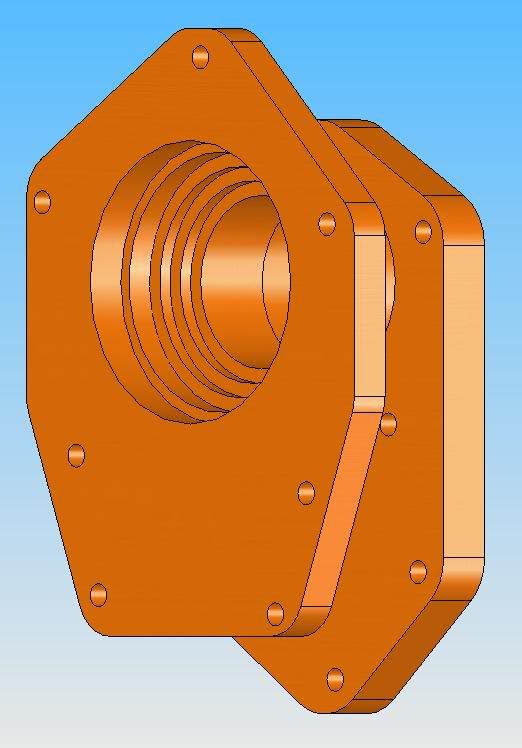
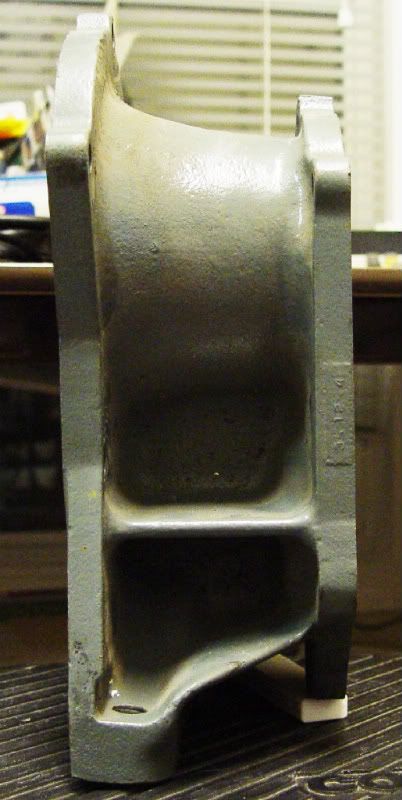
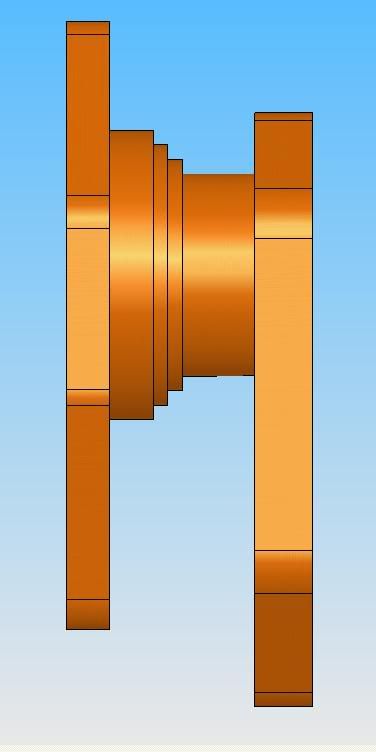